CORROSION MONITORING IN MARINE ENVIROMENT IN CROATIA
Writers: Prof. Dubravka Bjegovic, Ph.D., Faculty of Civil Engineering, University of Zagreb Irina Stipanovic, B.Sc.C.E., Faculty of Civil Engineering, University of Zagreb Marijan Skazlic, M.Sc.C.E., Faculty of Civil Engineering, University of Zagreb Kajo Feric, B.Sc.C.E., Croatian Institute of Civil Engineering, Center Split
2.2. Inspectionmethodology ontheoldstructure
The oldstructurewascomposedofreinforcedconcreteelements(columns)andprestressedreinforced concreteelements(beamsandT-girders),anditwasbuildintheearlyseventies.Duringtheyear 2001the investigation of theoldstructure was performed, whichsummary is following [1].
2.2.1. Visual structure inspection
On thedockconstructionelements,whichwere demountedandpulledoutfromthesea,primarilyavisual inspectionwasdone(Fig.3-6).Basedonthisvisualinspectionitwasconcludedthatthemainbeamsof thespanstructureare inthecriticalstateof damage(Fig.3-4),andnofuthertestingswereneededtoprove usabilityoftheseelements.Thecolumns ofthetesteddockwerecompletelycoveredwiththeshells (Fig.5-6), and on some places concretecoverwasdestroyedbythereinforcement corrosion (Fig.6).
On the drilled specimens from the structure chemical analysis were performed, which included chloride and sulphate content, pH value, carbonation. Test results are shown in next diagrams (Fig.7-8).
Figure 8. Sulphate profile through the depth of the concrete
After the final evaluation of the structure degradation level, the reparation proccess had started. In the spring 2002 a new marine was built, with prefabricated reinforced and prestressed concrete elements. All span structure elements and some columns were changed with new precast elements. The rest of the columns were left in the sea, since they didn`t show high degradation level. During production of beam elements for one of the docks (dock F) tiny cracks occured. Considering the agressive enviroment where they would be placed, a corrosion protection with migrating corrosion inhibitor (MCI® 2000) has been applied on the surface. Migrating Corrosion Inhibitors (MCI®) are used for the protection of reinforcing steel in concrete. They can be incorporated as an admixture or topically applied to the concrete surface. Migratory inhibitors are transmitted through concrete to the reinforcing steel by diffusion [2-3].
3.1. Monitoring purpose
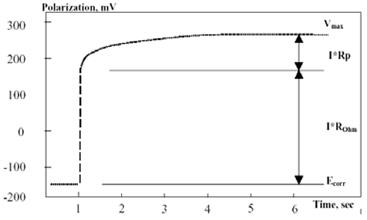
When the constant current Iappis applied to the system, the polarized potential of reinforcement
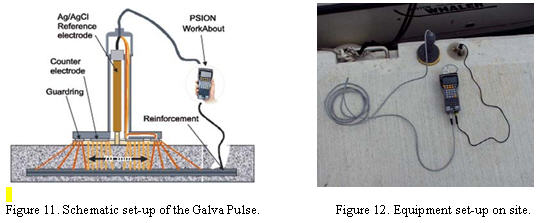
Dock B1 was built of the concrete quality C40. Span beams are prestressed prefabricated concrete elements, with U shape in cross section (Fig.9). Concrete surface was done without any protection. On Figure 13 the position of dock B1 is visible and that the first span beam is exposed to sea splashing. Schematic view of test points is are shown on the Fig. 14.
Duringthemonitoringthecorrosioncurrent,corrosionpotentialandconcreteresistivityweremeasured. On nextdiagrams themeasuring results fromdockB1areshown:
Span structure beams for the dock F (Fig. 21) are built with reinforced prefabricated concrete elements. As already described, these elements are treated with MCI inhibitor, after production. Schematic view of test points is shown on Fig. 22.
The estimation of the remaining service life based on the measured values of corrosion current can be done according Clear [7], as shown in Table 1.
Table 1.
Corrosion current Icorr[µA/cm2]
|
Corrosion damage
|
< 0.5 µA/cm2
|
no corrosion damage expected
|
0.5 < Icorr< 2.7 µA/cm2
|
corrosion damage possible in
10 to 15 years
|
2.7 < Icorr< 27 µA/cm2
|
corrosion damage expected
in 2 to 10 years
|
27 < IcorrµA/cm2
|
corrosion damage expected in 2 years or less
|
has to predicted for on site measuring.
5. Literature
Conference on Non-Destructive Testing; Rome, Italy, October 2000, pp. 642-652
המאמר באדיבות ניצוץ - ייעוץ לתעשייה טלפקס: 04-6772212
אין תגובות